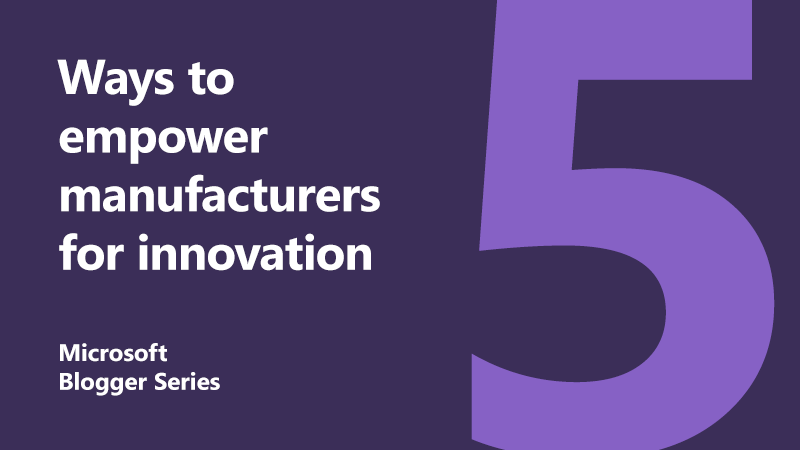
5 ways to empower manufacturers for innovation
Our latest report, Creating a blueprint for UK competitiveness, found that competitive benchmarks in the UK haven’t changed much since the 18th Century. The traditional methods of growth, often in rooted in productivity, don’t account for technology and the societal changes.
In manufacturing today, this is reflected in the complex proprietary systems that create data silos and slow productivity. Manufacturers must combine talent, technology, and future readiness to drive transformation, resilience and competitiveness in the new normal.
How can manufacturers become more innovative and deliver a sustainable future and competitive growth? By looking at unifying data and intelligent manufacturing and resources. Here are five ways you can get started.
1. Transform the workforce and empower innovation
Manufacturers often work across different sites. Frontline workers often need secure access while out in the field. Or perhaps, you have a hybrid workforce. To work in their best way, everyone needs the same secure access to their tools and apps, no matter where they are.
Combine productivity apps, intelligent cloud services and security to transform the way you work wherever you are. While the Ventilator Challenge UK was a unique scenario where 33 manufacturers came together to address the shortage of ventilators, the way they chose to work highlighted the power of technology.
By using Microsoft Teams, the Challenge found communication between everyone easy. They could collaborate on documents, have meetings, and share information as a single source of truth. With built-in security, data is protected in transit and at rest, meaning confidential proprietary information can be shared with confidence.
“It’s been absolutely invaluable as a collaboration tool. It saved so much time and confusion,” says Laura Shrieves, Head of Systems Engineering – Training Solutions at Thales, one of the participating engineering companies.
Another challenge manufacturers face is the ability to train and assist frontline workers from anywhere. This is where Microsoft Dynamics 365 Remote Assist and the HoloLens 2 can come in handy. With the help of this technology, manufacturers can now empower people to collaborate, solve problems in real time, access critical information while working and be able to walk through the site virtually. With Dynamics 365, the Ventilator Challenge were able to quickly train employees across different sites and deliver expert guidance when needed.
“We quickly realised that the HoloLens 2 could be used with the remote assist capability in order to get expertise and knowledge out of Smiths and Penlon, who have been building ventilators for many years. This was one of the big advantages,” says Shrieves.
2. Engage customers in new ways
By unifying your data across different silos (e.g. service, sales and marketing), you can drive value with insights and deliver personalised customer experiences, making you more agile and competitive in the market.
Automotive enterprise CNH Industrial, wanted to help customers optimise the use of their vehicles. They built a digital platform on Azure to collect insights that can give their customers information on how to save fuel or optimise their journeys. They can also then use this data to deliver better experiences and build better products, quickly.
“The platform may provide feedback to truck drivers on how to brake or accelerate differently. Such changes in driving style can save money on gas,” says Matteo Barion, Head of Digital Platform, DevOps & Quality Assurance at CNH Industrial.
3. Make the supply chain more visible and intelligent
When you make your supply chain intelligent with AI and IoT connected to devices and factories, you can improve resiliency, efficiency, traceability and profitability. When you build agile manufacturing and distribution processes you can deliver products on time, optimise resource planning, adapt to changing business models, and ensure business continuity while staying profitable.
Coats is one of the world’s leading industrial thread manufacturers and thus has global operations and a complex supply chain. By moving to Azure, they gained the flexibility and agility to optimise existing processes and accommodate for unexpected changes in operation.
By linking everything to an intelligent supply chain, Coats can minimise its environmental footprint while keeping up with demand. For example, they were able to fine-tune thread winding machines to ensure it only uses what it needs, and by moving to the cloud from on-premise data centres, they have been able to reduce their carbon footprint and now only use processing power when they need to.
“With Azure, we have the horsepower we need to hold to our timelines and get products through the manufacturing floor in an efficient manner,” says Helge Brummer, Vice President of Technology and Operations at Coats. “In some situations, the results have been dramatic. For example, sampling orders—which are an important part of customer decision-making—used to take 10 to 14 days to process. With the agility of the cloud, we’ve cut that to two days.”
4. Optimise plant and asset lifecycle
That brings us to our next way that manufactures can innovate by infusing operations with tech and industrial IoT you can drive reliability and quality whilst delivering safe and secure operations.
By leveraging machine learning and AI across factories, Ricoh can access greater insight through data to deliver greater value for customers. Ricoh can adjust machines in real time ensuring they are running at optimum and producing high quality products. They have also improved operational and cost efficiency by up to 10 times with predictive maintenance.
5. Drive new innovation and new services
Finally, by unifying data and harnessing the power of analytics and AI, you can uncover new business value from digital services and sustainable products that can transform the customer experience.
To increase supply chain transparency and implement innovative logistics solutions across plans, BMW Group started several logistic pilot programmes in their production lines. They developed automation kits, smart watch capabilities, and Smart Transport Robots.
This meant they were able to load and unload goods containers quicker, integrate scanners, displays and smartwatches to support employee logistics and utilise virtual reality to create spaces for planning and logistics of new plant sites.
“Logistics is the heart of our production system. Our broad spectrum of ground-breaking projects helps us run increasingly complex logistics processes efficiently and transparently,” says Jürgen Maidl, Head of Logistics.
Be ready for the new normal
Underpinning manufacturers ability for sustainable growth now and in the future is Manufacturing technology and industry expertise. The most important thing to remember about driving this change is to keep your people at the heart of any decisions. Unifying data and optimising processes across supply chains makes it easier for your employees to uncover insights, deliver personalised customer experiences and innovate with new products and services.
We work closely with manufacturing companies and industry organisations to ensure we are delivering genuine business outcomes through partnerships that bring together expertise in people, processes, and technology. We work closely with a number of the innovation centres, in particular the Advanced Manufacturing and Research Centre (AMRC), to help scale innovation across the manufacturing landscape. We’ve also worked with BMW Group to create the Open Manufacturing Platform (OMP). Designed to break down barriers through the creation of an open technology framework and cross-industry community, we’re supporting the development of smart factory solutions. The goal is to significantly accelerate future industrial IoT developments, shorten time to value and drive production efficiencies while addressing common industrial challenges.
This all connects to help manufacturers become more resilient, agile and ultimately more innovative. In the last year, we’ve learned to expect the unexpected and sustainable growth helps us manage this with confidence.
Find out more
Discover more about the resilient supply chain
Harness the power of data and analytics
About the author
Richard is responsible for leading Microsoft’s approach into the UK Manufacturing industry.
Richard joined Microsoft 14 years ago, where he has held various leadership roles across the business, the most recent of which is to establish and drive Microsoft’s strategy into the UK Industrial sector. He works closely with businesses and partners across automotive, aerospace, and manufacturing focussing on how digital transformation can enable them to achieve more.
He also works closely with associated industry bodies and consortia, supporting industry collaboration, growth and skills development.
Richard holds a Bachelor of Arts Degree in Accounting.
Join the conversation at Envision
Digital technology is changing not just how organisations operate but how leaders lead. Join us at Envision, where executives across industries come together to discuss the challenges and opportunities in this era of digital disruption. You’ll hear diverse perspectives from a worldwide audience and gain fresh insights you can apply immediately in your organisation.
Connect with leaders across industries to get relevant insights on leadership in the digital era.