
デジタルとリアルの融合がプロジェクトを加速する。石油化学業界向け DX 推進セミナー『製造現場に変革をもたらすデジタル技術の活用と推進のポイント』参加レポート

設備の老朽化や世代交代が進む化学プラントでは、安全性や生産性を向上させるために DX の推進が求められています。DX を成功させるには、単なる技術の導入や刷新ではなく、正しくデジタル技術の動向を理解し、自社の課題に適した技術を取り入れ、社員の育成や意識改革を行う必要がありますが、なにから手をつけるべきか迷っている企業も多いのではないでしょうか。
こうした課題の解決を目指す石油化学業界の企業を対象として、デジタル技術の活用や推進のポイントを紹介し、さらに参加者同士が交流できるイベントとして、2022 年 10 月 18 日 (火) に川崎で、26 日 (水) に岡山で、石油化学業界向け DX 推進セミナー『製造現場に変革をもたらすデジタル技術の活用と推進のポイント』が開催されました。
コロナ禍で顔を合わせて語り合う場が減少した昨今、近隣の同業他社との課題共有や情報交換を行うネットワーキングがプログラムに含まれていたこともあり、川崎会場には 30 名の定員いっぱいの参加者が訪れました。

予測不可能な時代を乗り越えるために、どう AI と向き合うか
プログラムは、東京農工大学 工学部 化学物理工学科 教授の山下 善之氏による『デジタル技術を駆使した 化学プラントの運転・保守』と題されたセッションで幕を開けます。
まず山下氏は、天災やパンデミック、軍事侵攻といった想定外のできごとが世界中で起き、人工知能やバイオテクノロジーが予想をはるかに超えて進化している VUCA の時代において、「今まで常識だと思っていたことが常識ではなくなってしまう時代にどういうことを考えるべきでしょうか」と参加者に問いかけます。

続けて「いくらでもデータを蓄えられる今の時代に重要とされるのはビッグデータの活用であり、ものづくりの現場においては“サイバーフィジカルシステム”が重要な概念になる」と語ります。サイバーフィジカルシステムとは「デジタル空間に蓄えられたビッグデータを、AI などを使って解析し、その結果が IoT で実世界につながって、リアルタイムに反映される循環」のこと。山下氏は、「サイバーフィジカルシステムが実現できたことから、今いろいろなところで“スマート工場”が実現しつつある」と、製造業界における DX の現在地を解説します。
さらに、第 3 次 AI ブームと言われる今、これまでの常識を覆すインパクトを持った AI ソリューションが多数開発されていることから、これまでのブームとは異なり、AI の進化が止まることはないだろうと予測。重要な視点として、AI に任せきるのではなく人間が介在することで精度が上がる場合が多いことから、「人間とコンピュータの協働が重要」と分析。リアルとデジタル、ヒトとコンピュータのコラボレーションが、予想不可能な時代を乗り越えるひとつのカギになることを示唆しました。

ここから山下氏の話は本題の化学プラントのデジタル化へ。我が国のデジタル化の現状として、2021 年には 81%の企業が DX を計画、そのうち 7 割以上が実際に取り組んでいるというデータを示し、生産性の向上やコスト削減などを期待して、すでに多くのデジタル化事例が報告されていると語ります。
ここで山下氏は、化学プラントが DX を進めるための支援策として、経済産業省の「スマート保安」に向けた取り組みを紹介。カメラ搭載ドローンによる検査を可能とする規制改正や、AI を使ったシステムの信頼性を評価するガイドラインの策定、日タイスマート保安コンソーシアムの設立など、経済産業省主導でさまざまな取り組みが行われており、化学プラントの運転・保守における AI 適用事例が紹介されている「Smart Industrial Safety Digital Catalog」や、デジタル化のどの段階でどの技術を採用すべきか、将来を見越した計画を立てられる「高圧ガス保安分野スマート保安アクションプラン」などが用意されていることを示します。
続いて山下氏は、化学プラントのデジタル化に伴って想定される課題とその解決策について言及。データ不足に伴うシミュレーション結果の信頼性という課題については、シミュレータや物理モデルの併用が有効であるとし、機械学習のブラックボックスのモデルと物理モデルのホワイトボックスをつないだグレイボックスモデルの作成や、シミュレーションと並列で動作させるデジタルツインの活用などをその例に挙げます。
人材育成については、化学プラントにおいてはデータサイエンスの知識だけでなくプラントや計測制御の知識が必要であり、「データサイエンティストがプラントについて学ぶよりも、プロセス技術者がデータサイエンスを学ぶ方をお勧めします。データサイエンスの技術は今非常に使いやすくなっていますから」とひとつの方向性を示しました。
最後にまとめとして山下氏は、「AI は進歩を続けており、多くの分野で適用が当たり前となるなかで、多くの課題が出ていることも事実。ですがスマート保安の推進など解決策も用意されているので、ぜひ活用してほしいと思います」と述べ、日本の製造業が競争力を保つために、デジタル化は不可欠なことを強調してセッションを終了しました。
ありたい姿から逆引きして“現場のデジタル武装”を進める
続いて登壇したのは、日本マイクロソフト エンタープライズ事業本部 製造営業統括本部 インダストリーアドバイザー 安並 裕。『製造現場に変格をもたらすデジタル技術の活用と推進のポイント』と題して、化学プラント内の情報を利活用するポイントについてのセッションが行われました。

安並はまずデジタル化の変遷から語り始めます。2000 年代初頭から、先進的な分野では IT (Information Technology) 側の情報と OT (Operational Technology) 側の情報の連携、いわゆる IoT の重要性は認識されていたものの、当時の日本の化学系企業からはあまり関心を持たれませんでした。2010 年頃になるとスマートフォンやドローンといったさまざまなデバイスが出現して、アナログのデジタル化が進み、さらに近年になると、デジタルツインや AI によるダイナミック解析、自動運転などの技術が現実化してきました。
この先の未来について安並は「局所的なプラントがデジタル化されてデジタルツインと呼ばれるものができてきた。その先には近隣のプラントや自分の会社の別工場との連携が進むのではないか」とし、閉じた世界ではなく、多くの企業が情報や知見を共有し合う世界がくるはず、と予測します。
「ただ、まだまだ化学プラントにおいてはデータが散在しており、多くの課題があります」と安並。その理由として、さまざまな思惑からツールが個別で導入され、情報がサイロ化してしまっていることを挙げます。安並いわく、デジタルプラントとは「とにかくサイロ化しないこと。また Google マップのようにレイヤーとなっていろいろな情報が浮かび上がってくる世界。それから予測型であること。過去のデータを蓄積しておくだけではなくて、先々を予測しながら操業できること」。これがデジタルプラントのあり方であり、デジタルプラントを構成するためには“縦と横の情報連携”が大切であることを示します。

まずは縦の流れにおいては、制御、計装から計画、実績、分析までの情報連携を想定し、関連業務と各種データがシステム連携する仕組みづくりを行うこと。そして横の流れでは、市場調査から各工程を経て顧客からのフィードバックを得るところまで業務を長期的に見たときに、品質不良の原因が存在した製造工程の特定時刻、特定パラメータの動きまで、トレーサビリティ (追跡可能性) を確保すること。
「この縦と横の情報連携を表現するのが、実際のプラントをコンピュータ上で模擬的に示したもの、すなわちデジタルプラントあるいはデジタルツインと呼ばれるものになります」と安並。このデジタルプラントに実プラントと全く同じものが表現される仕組みを実現できれば、さまざまな自動化や合理化につながるというわけです。


続いて安並は、本セミナーの協賛企業であるアバナード、Cognite、Hexagon といったパートナー各社が Microsoft Azure をプラットフォームとして構築したシステムが、デジタルプラントの構築に大きく貢献できることに言及。そのひとつの例として、アバナードがパートナー企業とともに Microsoft Azure 上に構築した大規模な情報共有プラットフォームによって、東南アジアのベテランの少ない現場で安全・安定操業を続けるための仕組みを可能にした事例を挙げ、マイクロソフトの製品を軸にしつつ、業界固有の各種ソフトウェアを連携させることで、デジタルプラントの実現に近づけることを示しました。

ここから話はデジタル化の進め方へと展開します。ここ 2〜3 年の体感として安並は、「ギアは 1 速から 2 速へ上がったことを感じるけれども、3 速、4 速、ましてや 5 速に入っている企業は少ない」と、デジタル化はまだ始まったばかりという見解を示します。その理由として、「どういうことをしたいのか、どんな姿になりたいのかといったゴールがあいまいなまま走り始めていることが多いのではないか」と分析。カイゼンから脱却して改革 (トランスフォーメーション) の意識を持つこと、3 年ごとの中期経営計画のスピード感覚ではなく四半期ごとの試行錯誤を繰り返すこと、ある程度割り切って予算をかけることをポイントに挙げます。そして「未来のありたい姿を、若手も含めて議論する場を設け、出てくるアイデアを切り捨てずに議論していただきたいと思います」と、保守的な業界の変革を進めるためのアドバイスを送りました。


最後に安並はプロジェクトの進め方について、「点ではなく線でつながるロードマップをつくることが大切であり、ありたい姿からどういう順序で逆引きすれば実現できるのかを考えることがポイント」と語り、業務上のインパクトの大きさと業務戦略を XY 軸として施策をマッピングし、実現するための技術やソリューションを当てはめていく方法を例示します。そしてその技術やソリューションは、マイクロソフトがパートナー企業とともに支援できることを伝え、「私は、現場の方が迷うことなく正確に作業できる、“現場のデジタル武装”がひとつの最終形だと考えています。世の中にあるいろいろなソフトウェアやデバイスをうまく組み合わせて情報を連携させる観点で、プロジェクトを進めていただければ」と言葉を結びました。
現場 DX を推進するテクノロジーの最新事情とは
休憩をはさんで後半は、協賛 3 社によるセッションが行われました。3 社は会場内に設置されたブースで製品案内やデモを行なっており、セッション前にブースで対話していた参加者も多かったようで、興味深く発表を見守っている様子でした。

まずはアバナード株式会社の玉水 大貴氏が登壇。『Digital Twin による工場最適化ソリューション』と題して、デジタルツインを活用した工場の最適化について解説しました。
玉水氏は、デジタル上に再現された「Intelligent Factory」というソリューションを紹介。Intelligent Factory はこれまでバラバラだった情報を活用し、機械、生産ライン、工場のプロセスを最適化するためのものであり、それぞれ Machine Twin、Production Line Twin、Factory Twin と名付けられたデジタルツインを用いて、製造工程におけるあらゆるステイタスのシミュレーションを行い、最適化を図ることができます。
続いて玉水氏は、これらの最適化を行うために実際どのようなロードマップを描くべきかを解説。早期、中期、長期、そして最終構想で期間を区切って、テクノロジー、働き方、人材・組織、エコシステムの 4 つのジャンルで行うべきことをマッピングすることで、それぞれの期間にクリアすべき課題が見えてくることがわかります。「これがすべてに当てはまるわけではありませんが、ぜひ参考にしてみてください」と呼びかけてセッションを終了しました。

続いては、Cognite 株式会社の江川 亮一氏が登壇。『海外のデジタルツイン活用事例から学ぶ、現場の見える化・リモート化』と題して、同社の持つ Data Ops ソリューションについて紹介を行いました。
江川氏は DataOps の能力として「組織内の誰もが必要なデータにアクセスでき、活用できる」「現場のプラント専門家やエンジニア自身が、データを可視化するダッシュボードを簡単に開発できるようになる」「省人化、無人化、自動運用ロボットによる点検・メンテナンス作業により業務を効率化。高度なスキルを保つ人材の能力を活かせる」「AI を活用したプロアクティブな実施作業のプランニングを実施し、作業負荷を下げていく」ことを挙げ、「ひとつのユースケースのためにあるものではなく、さまざまな観点で使えるもの」とその汎用性をアピールします。
続いて江川氏は、「Cognite Data Fusion (CDF)」を紹介。CDF は IT、OT、ET データと接続するためのコネクタであり、工場内からデータのコピーを集めてきてプラットフォーム上で関連づけすることで、企業にとって大きな負担であるデータのクレンジング作業を削減し、すぐに業務に生かすためのソリューションです。米国の石油化学企業 Celanese 社の事例動画では、CDF を活用して業務の最適化を成し遂げた様子がわかりやすくまとめられており、参加者は興味深く見入っていました。

最後に登壇したのは HEXAGON のアセットライフインテリジェンス部門の日本法人である日本インターグラフ株式会社の田代 弘二氏。『HxGN SDx のご紹介』と題してセッションを行いました。
同社は製造業向けソリューションの整備に力を入れており、なかでも設備保全管理分野に重きを置いて事業を推進しています。今回紹介された HxGN SDx は、設備保全管理業務のうち文書管理と設計図書管理業務を支援するソリューション。設計図書や、仕様書などの設計ツール以外のものから発生する一次元の図書も管理できるようになります。
田代氏は、設備情報管理が必要な理由として「設計の段階からいくつも同じようなファイルが存在することでどれが正しい情報かわからなくなり、設備情報としての信頼性が損なわれてしまうため、プラントが正常に操業できている保証がなくなってしまう」ことを挙げます。HxGN SDx は、P&ID やデータシート、MTR といった図書の情報をすべてオブジェクトとして抽出して一元管理することで、常に最新の情報を簡単に検索、閲覧できるように管理するツールです。タグから属性情報を見たり関連情報に遷移したりすることも可能です。
田代氏は実際に画面上で各システムと連携させて活用するデモを提示。指図に必要な図書を呼び出して必要なワークパッケージをつくるなど、日々の業務で HxGN SDx を生かせることがわかります。「HxGN SDx は Web ツールのため、タブレットを持っていけば現場から操作することもできます。管理する側も現場で作業する側も、シームレスに情報を共有できるツールです」とアピールしてセッションを終了しました。

リアルな対話と体験にこそデジタル化のヒントが潜んでいる
協賛 3 社のセッション終了後はふたたび山下氏と安並が登壇して、質疑応答およびディスカッションが行われました。「AI ツール選びはどのように行えばよいか?」という質問に対して山下氏は「ツール選びより何をやりたいか、どんなことがやりたいか。そちらが決まるとツールは自ずと決まってきます」と回答。「人材育成において全社員がやっておくべき基礎教育のレベルは?」という質問への「極端に言えばスマートフォンを使えればいい。デジタルが当たり前の文化をつくることが大事」という回答には会場から感嘆の声が上がっていました。
こうして大いに盛り上がったセッションはすべて終了。続いて、部屋を移して参加者、講演者、協賛企業が交流するネットワーキングが行われました。久しぶりのリアルでの交流の場とあって、協賛企業のブースで説明を聞いたり登壇者を囲んで談笑したりと会場は熱気に溢れ、Hololens 2 による遠隔作業支援を疑似体験できる「ウェアラブルデバイス体験」には行列もできていました。
山下氏がセッションのなかで「AI と人間の協働が大切」と語ったとおり、デジタル化を推進する議論をリアルな対話と体験によって深化するプロセスは、参加者にとって今後のプロジェクトを進めるうえでの大きなヒントとなったに違いありません。

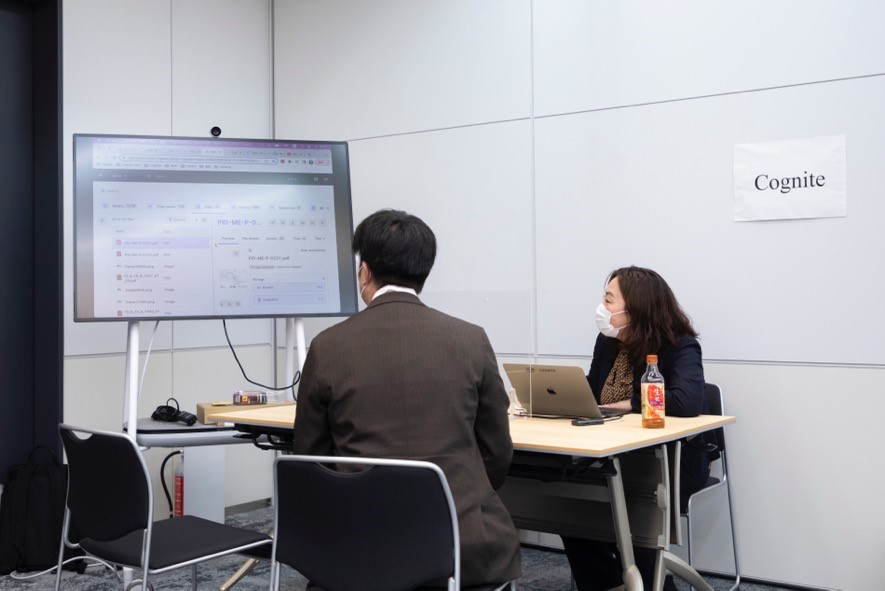


